Uncover the benefits of plastic extrusion in product development
Uncover the benefits of plastic extrusion in product development
Blog Article
Secret Advantages and Factors To Consider of Applying Plastic Extrusion in Your Projects

Understanding the Basics of Plastic Extrusion
Plastic extrusion, a staple in the production market, is a procedure that entails melting raw plastic product and reshaping it right into a continuous profile. The appeal of plastic extrusion exists in its flexibility. The choice of plastic and the design of the die figure out the product's attributes.
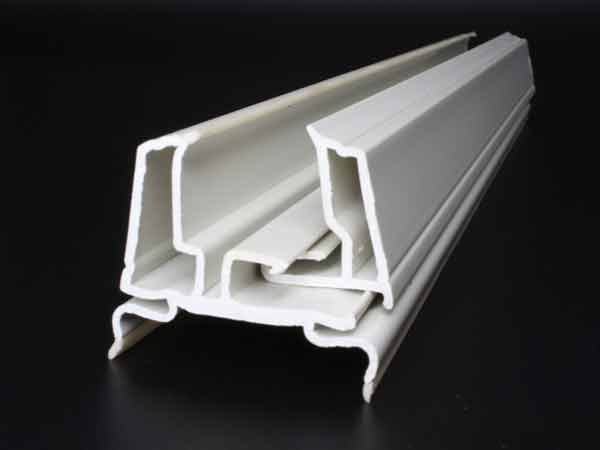
The Economic Benefit of Plastic Extrusion
The economic advantage of plastic extrusion exists primarily in 2 areas: economical product manufacturing and helpful manufacturing rates. With plastic extrusion, services can generate high volumes of product at a lower expense compared to other approaches. The procedure boasts an outstanding manufacturing rate, significantly decreasing time and more improving its financial feasibility.
Cost-efficient Material Manufacturing
A considerable advantage of plastic extrusion is its impressive cost-effectiveness. Additionally, the extrusion procedure permits for a high level of accuracy in shaping the plastic, minimizing the need for pricey post-production alterations or modifications. All these elements make plastic extrusion a highly economical option for several jobs, offering an attractive balance between cost and efficiency.
Beneficial Manufacturing Speeds
While maintaining the cost-effectiveness of the materials, another noteworthy advantage of plastic extrusion lies in its rapid production rates. This mix of rate, cost-effectiveness, and high quality underscores the significant economic benefit of applying plastic extrusion in various jobs.
Adaptability and Personalization: The Toughness of Plastic Extrusion
One of the famous toughness of plastic extrusion hinges on its versatility and customization possibility. These qualities unlock to unrestricted design opportunities, offering manufacturers the ability to customize products to particular demands. This increased degree of modification not just improves product capability but also substantially increases item uniqueness.
Unrestricted Layout Possibilities
Plastic extrusion radiates in its capability to use virtually infinite layout possibilities. This method offers liberty to develop intricate profiles and intricate shapes, an accomplishment hard to attain with other manufacture methods. Owing to the fluid nature of liquified plastic, the process is flexible sufficient to generate a diverse range of dimensions, forms, and dimensions. The plastic can be manipulated to match one-of-a-kind specs, enabling the manufacturing of customized geometries and meeting certain client needs. Plastic extrusion can manage a variety of plastic kinds, broadening its application scope. This adaptable strategy, for that reason, serves a large range of industries from construction to auto, packaging to electronic devices, and beyond. With plastic extrusion, the layout possibilities are essentially limitless.
Enhancing Item Individuality
The versatility of plastic extrusion can substantially improve product originality. This procedure permits designers to explore different forms, dimensions, and colors, offering them the freedom to develop distinct look at more info items that attract attention in the market. It is this personalization that lends a distinctive identification per product, differentiating it from its competitors.
Along with its aesthetic benefits, the customizability of plastic extrusion also supplies sensible benefits. Designers can modify the buildings of the plastic according to the certain needs of the application, improving the product's capability. For example, they can make the plastic extra flexible, a lot more resilient, or much more immune to warm, depending explanation upon what the product requires. Hence, plastic extrusion not just enhances product uniqueness but likewise its utility and bankability.
Design Limitations in Plastic Extrusion: What You Required to Know
How can develop restrictions potentially influence the process of plastic extrusion? While plastic extrusion is functional, style restrictions can cut its advantages. Certain complicated styles might not be practical because of the constraints of the extrusion procedure, possibly restricting the development of detailed profiles. The procedure is less suitable for hollow or multi-chambered structures. In addition, the extrusion procedure might not constantly supply the preferred surface area coating, particularly for those calling for high gloss or optical clarity. Product choice can additionally position difficulties, as not all polymers are suitable for extrusion. High-temperature resistant plastics, for instance, might present troubles. Recognizing these constraints is crucial for reliable execution of plastic extrusion in your projects. plastic extrusion.
Evaluating the Environmental Impact of Plastic Extrusion
While recognizing layout limitations is a considerable element of plastic extrusion, it is similarly important to consider its environmental effects. The procedure of plastic extrusion involves melting plastic products, potentially releasing dangerous gases into the environment. Further, the resulting items are frequently non-biodegradable, adding to land fill waste. Advancements in technology have enabled for even more environmentally-friendly techniques. For instance, using recycled plastic products in the extrusion procedure can minimize environmental effect. In addition, creating eco-friendly plastic alternatives can aid reduce waste issues. Evaluating these environmental elements is vital when carrying out plastic extrusion projects, guaranteeing an equilibrium in between performance, cost-effectiveness, and environmental obligation.

Situation Study: Successful Projects Making Use Of Plastic Extrusion
Success tales in the area of plastic extrusion are plentiful, demonstrating both the adaptability and effectiveness of this manufacturing procedure. plastic extrusion. One more effective case is the manufacturing of plastic film for product packaging and farming. These instances illustrate plastic extrusion's critical duty in various fields, attesting to its versatility, cost-effectiveness, and reliable result.
Final thought
Finally, site plastic extrusion provides a economical and efficient technique for generating intricate forms with marginal waste. While it gives various benefits such as cost-effectiveness and convenience, it's important to take into consideration possible design constraints and ecological impacts. Applying biodegradable or recycled materials can mitigate these issues, improving sustainability. Integrating plastic extrusion right into jobs can bring about successful outcomes, as shown by numerous case studies.
Plastic extrusion, a staple in the production market, is a process that entails melting raw plastic product and improving it right into a constant profile. Plastic extrusion can manage a range of plastic types, expanding its application scope.How can design constraints possibly impact the procedure of plastic extrusion? The procedure of plastic extrusion involves melting plastic materials, possibly launching damaging gases right into the environment. Making use of recycled plastic materials in the extrusion procedure can lower environmental impact.
Report this page